FAQ
Fragen und Antworten
In der EN 14610 [1] und der DIN 1910-100 [2] wird das Schweißen als ein Verfahren definiert, bei dem Bauteile durch den Einsatz von Wärme und /oder Druck dauerhaft miteinander verbunden werden. Auch ein Vorteil, dass das oft ohne zusätzliche Schweißmaterialien erfolgen kann. Dabei wird den Werkstücken von außen Energie zugeführt. Das Material verflüssigt an der Verbindungsstelle. Um optimale Schweißbedingungen zu erreichen, kommen oft Hilfsstoffe wie Schutzgase, Schweißpulver oder Pasten zum Einsatz. Die Kombination aus intensiver Wärmezufuhr und gegebenenfalls einem gleichzeitigen Druck sorgt für eine feste, unlösbare Verbindung der Bauteile.
Ja, es gibt das Lasertiefschweißen. Hierbei wird ein hochenergetischer Laserstrahl eingesetzt, um eine tiefe, schmale Schweißnaht zu erzeugen. Der Laser erhitzt das Material an der Verbindungsstelle so intensiv, dass es über eine beträchtliche Tiefe schmilzt und eine homogene Verbindung bildet. Diese Methode zeichnet sich durch eine sehr geringe Wärmeeinflusszone, hohe Präzision und schnelle Bearbeitung aus – ideal für anspruchsvolle Anwendungen in der Serienfertigung. Beim Laserschweißen mit intensiv fokussiertem Laser entsteht ein sogenannter Keyhole – ein Hohlraum, der durch Dampfkapillaren (gefüllt mit teilionisiertem Metalldampf) gebildet wird. Insbesondere bei Stahl, typischerweise bei 2–4 MW/cm² und einer Geschwindigkeit von etwa 1 m/min, verläuft die Schmelzzone tief und schmal. Dieser Effekt erhöht die Absorption der Laserenergie und führt zu einem größeren Schmelzvolumen.
Ja, beim Laserschweißen wird oft Schutzgas eingesetzt. Das Gas schützt die Schweißnaht vor Oxidation und Verunreinigungen und sorgt für eine stabile Schweißatmosphäre. Typische Gase wie Argon oder Stickstoff können auch dazu beitragen, das Keyhole zu stabilisieren und die Qualität der Verbindung zu verbessern. Zur weiteren Erklärung: Ein wesentlicher Vorteil des Laserschweißens ist die minimal gehaltene Wärmeeinflusszone. Dies wird durch sehr kurze Impulse (5–10 ms) und eine Pulsfrequenz von 10 Hz erreicht, was die Wärmeeinbringung reduziert. Bei sehr kleinen Werkstücken kann dennoch eine Überhitzung auftreten, sodass hier ein geeignetes Schutzgas zugeführt werden muss, um Verformungen zu vermeiden.
Beim Laserschweißen treten in der Regel nur minimale Einzugs- und Verzugserscheinungen auf. Die schmale Wärmeeinflusszone minimiert thermische Verformungen, sodass bei korrekter Prozessführung meist keine nennenswerten Probleme entstehen. Zur weiteren Erklärung: Ein Schweißverfahren ohne Einzug oder Verzug ist theoretisch nicht realisierbar. Allerdings minimiert das Laserschweißen diese Effekte so weit, dass sie die Werkstückqualität kaum beeinträchtigen. Der Randbereich der Schweißnaht wird dabei wesentlich durch den Fokusdurchmesser und die Energiedichte bestimmt. Dadurch verbessert sich die Maßstabilität, was die Weiterverarbeitung erleichtert, Nacharbeitszeiten verkürzt und die Produktionskosten senkt.
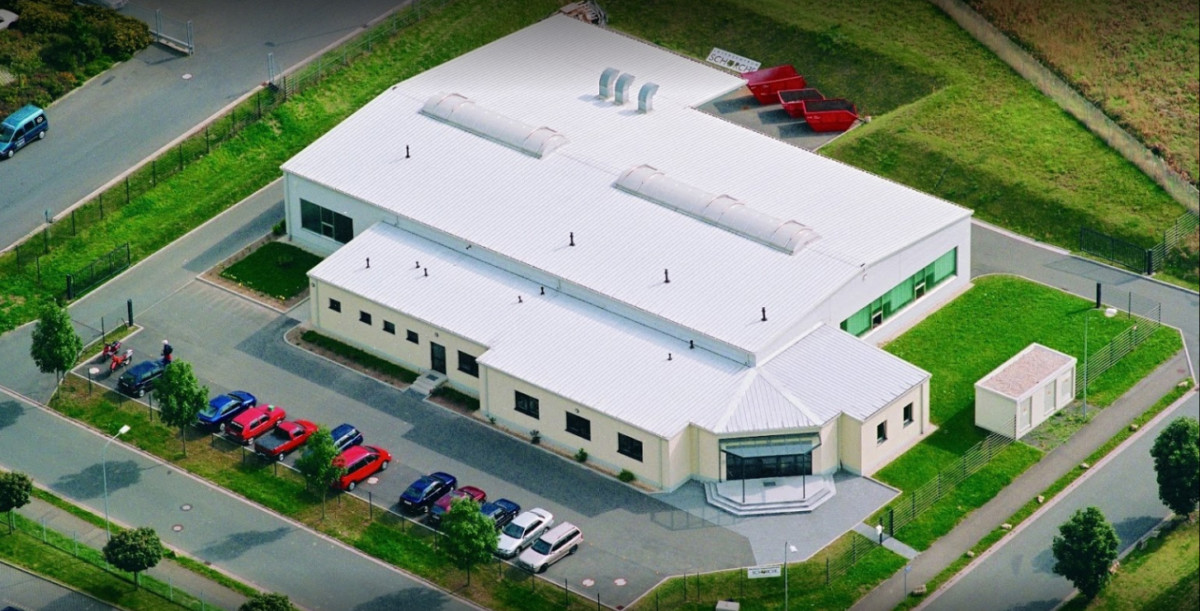
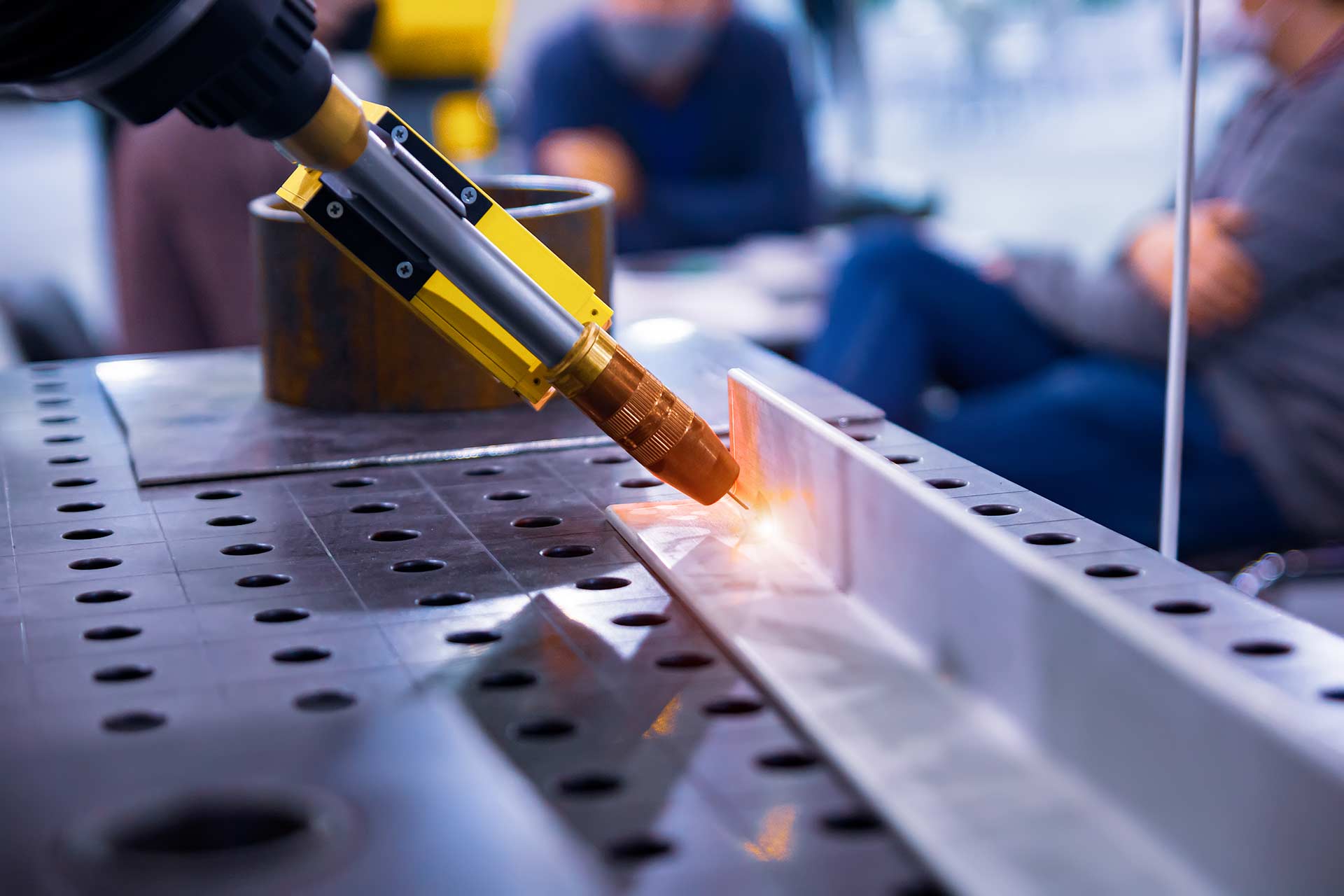